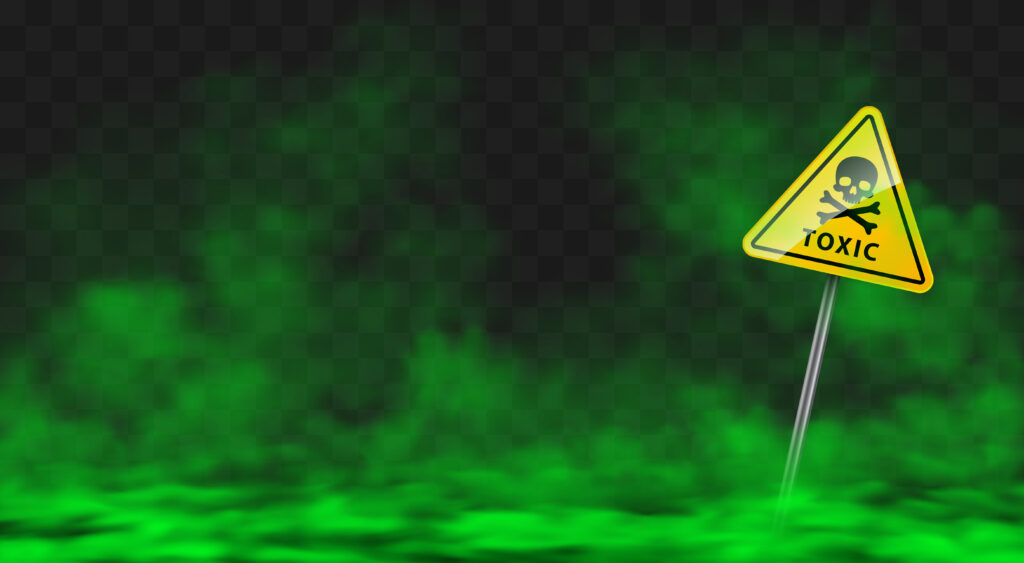
As a wholesale supplier, it’s essential to ensure that your workplace is safe and free from hazardous substances. That’s where Control of Substances Hazardous to Health (COSHH) regulations come in. In this article, we’ll provide you with a comprehensive guide to COSHH that can help you keep your workplace safe and compliant with the regulations.
What is COSHH, and Why is it Important?
COSHH, which stands for Control of Substances Hazardous to Health, is a set of regulations created by the UK government to ensure the safe handling, storage, and use of hazardous substances in the workplace. The COSHH regulations aim to protect workers from exposure to hazardous substances that can cause serious health problems, such as respiratory problems, skin irritation, and even cancer.
Under COSHH, employers have a legal obligation to assess the risks associated with handling hazardous substances in the workplace, and take appropriate measures to protect their workers. This includes providing adequate information, training, and protective equipment to employees, as well as implementing safe working practices and procedures.
COSHH is an essential aspect of workplace health and safety, as exposure to hazardous substances can have serious consequences for both workers and employers. Not only can it lead to long-term health problems for employees, but it can also result in legal action against employers if proper precautions are not taken.
In short, COSHH is important because it helps to ensure the safety and well-being of workers, while also helping employers to meet their legal obligations and avoid costly legal action.
Identifying Hazardous Substances
Identifying hazardous substances is a crucial step in ensuring the safety of workers and others who may come into contact with them. A hazardous substance is any substance that has the potential to cause harm to health, safety, or the environment. These can be found in many different forms, including solids, liquids, gases, vapours, dust, and fumes.
Identifying hazardous substances in the workplace can be done in several ways. One way is to check the material safety data sheet (MSDS) for each substance used or stored in the workplace. An MSDS is a document that contains information about the physical and chemical properties of a substance, its potential hazards, and the precautions that should be taken when handling it. MSDSs should be readily available for all hazardous substances used in the workplace.
Another way to identify hazardous substances is through workplace risk assessments. A risk assessment involves identifying hazards in the workplace and assessing the risks associated with them. This can be done by observing the work processes and practices, reviewing MSDSs, and consulting with workers who use or handle the substances. The results of the risk assessment should be used to develop safe work practices and control measures to minimize exposure to hazardous substances.
Training and awareness are also essential in identifying hazardous substances. Workers should be trained to recognize the potential hazards associated with the substances they work with and be aware of the appropriate safety measures to take. They should also be instructed on how to read and interpret MSDSs and how to report any unsafe conditions or incidents involving hazardous substances.
COSHH Risk Assessment and Control Measures
After identifying hazardous substances in the workplace, the next step in complying with the Control of Substances Hazardous to Health (COSHH) Regulations is to conduct a risk assessment and implement control measures to prevent or reduce exposure to these substances.
A COSHH risk assessment involves identifying the risks associated with the use of hazardous substances and evaluating the potential harm they can cause to workers and others who may come into contact with them. It is essential to conduct this assessment regularly as part of an ongoing health and safety management system.
There are five main steps in conducting a COSHH risk assessment:
- Identify the hazardous substances: This includes identifying all the substances in the workplace that may pose a risk to health. This can be done by reviewing safety data sheets, product labels, and carrying out workplace inspections.
- Identify who may be exposed: It is essential to identify all employees who may be exposed to hazardous substances during their work activities, including those who work with the substances directly and those who may be in the vicinity.
- Evaluate the risks: Evaluate the risks associated with exposure to the hazardous substances identified in step 1. This involves considering the concentration, duration, and frequency of exposure and the potential harm that exposure may cause.
- Implement control measures: Once the risks have been identified, it is essential to implement control measures to prevent or reduce exposure to the hazardous substances. These measures may include engineering controls such as ventilation, administrative controls such as safe working practices and personal protective equipment (PPE), such as gloves and respiratory protection.
- Monitor and review: Regularly monitor and review the control measures to ensure they remain effective in preventing or reducing exposure to hazardous substances. This involves reviewing and updating risk assessments and safe working procedures as necessary.
Implementing control measures is a critical aspect of COSHH compliance. The level of control measures required will depend on the nature of the hazardous substance, the level of exposure, and the potential harm it can cause.
Accessible COSHH Training Online
In addition to performing a COSHH risk assessment and implementing control measures, it’s essential to provide adequate training to all employees who handle hazardous substances. This training should cover the identification and handling of hazardous substances, as well as the correct use of any control measures that have been put in place.
One convenient and accessible option for COSHH training is online training courses. These courses can be taken by employees at any time and from any location, as long as they have access to a computer or mobile device and an internet connection.
Online COSHH training courses typically cover the following topics:
Introduction to COSHH: This section provides an overview of COSHH, including what it stands for and why it’s important.
Identification of hazardous substances: This section covers how to identify hazardous substances, including the different types of hazards and the symbols and labels used to indicate them.
Risks and effects: This section covers the risks associated with hazardous substances, as well as their potential effects on health and safety.
Control measures: This section covers the various control measures that can be implemented to minimize the risks associated with hazardous substances.
Personal protective equipment (PPE): This section covers the use of personal protective equipment, including what types of PPE are available and when they should be used.
Emergency procedures: This section covers what to do in the event of an emergency involving hazardous substances, including spillages, fires, and explosions.
Record keeping and monitoring: This section covers the importance of keeping records and monitoring the use of hazardous substances to ensure that control measures are effective and up to date.
By providing accessible COSHH training online, wholesale suppliers can ensure that all employees have the necessary knowledge and skills to handle hazardous substances safely and effectively. This can help to prevent accidents and injuries in the workplace, as well as ensure compliance with health and safety regulations.
Conclusion
As a wholesale supplier, ensuring workplace safety is crucial to protect your workers’ health and well-being. By following the COSHH regulations, identifying hazardous substances, conducting a COSHH risk assessment, and providing accessible COSHH training online, you can create a safer and healthier workplace for your workers.